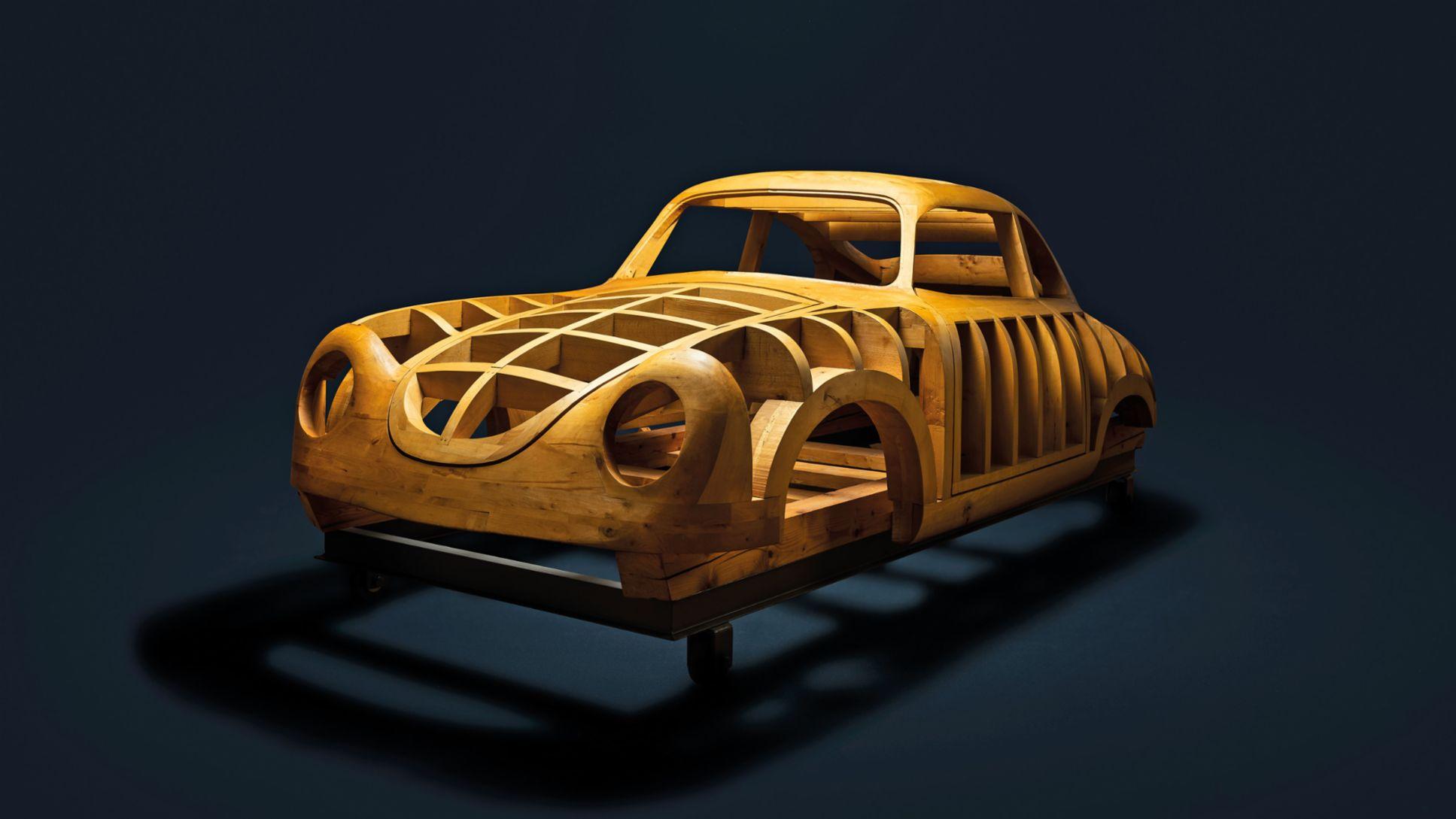
The original frame of the Porsche 356. The frame was used as a template for future metal bodies. A time-consuming process of trial and error, the steps were repeated over and over again until the doors, hoods, roof, and fenders fit the wooden model perfectly.
Photo By Heritage and Porsche Museum
Building a hydroplane myself makes one appreciate the skills involved when I see an article like this. The idea of hammering aluminum sheets to form body panels reminds me when I see aluminum cowlings on an old school hydro (before fiberglass came to be). That’s the reason why I am sharing this story that was recently published from the Woodworking Network.
The first Porsche 356 were manufactured by hand. A massive framework of ash wood served as inspiration for the iconic form.
Opened by Helmut Pfeifhofer in 1982, Porsche Automuseum in Gmünd is home to the original model, a massive framework of ash wood that served as inspiration for the first-ever 356 sports car, which was manufactured by hand 75 years ago – also in Gmünd, Austria.
This piece of history was referred to as “Holzklopfmodell” or, in German, hammered wooden frame, but the frame itself was never hammered. Rather, it served as a model for the vehicles that began rolling off the production line at the Porsche factory in Gmünd, Austria, in 1948. A total of 52 type 356/2 vehicles were produced, of which there were 44 Coupé and eight Cabriolet. There were also an additional eight to ten, later designated as superlight (SL), vehicle bodies. These were, however, not completed until 1951/52 by the racing department in Stuttgart.
75 years ago, Porsche was a manufacturing company based on the division of labor, with series production still in the distant future. While the steel chassis could be produced comparably quickly, the external bodywork process proved to be arduous, as the aluminum sheets had to be shaped using hammers and then repeatedly held up to the wooden frame for comparison.
A time-consuming process of trial and error, the steps were repeated over and over again until the doors, hoods, roof, and fenders fit the wooden model perfectly. It took a specialist at least 90 hours to perfectly form the 356’s unmistakable outer skin. Then – and only then – was it ready to be nailed, riveted, and bolted to the inner structure. For this reason, Porsche engaged specialists such as Kastenhofer, Keibl, and Tatra in Vienna, and Beutler in Thun, Switzerland, to help with the manufacture of the bodywork.